Investment Casting Process
Investment casting is a casting technique. It involves injecting liquid wax into a metal mold to create a wax pattern that is identical to the desired casting. Subsequently, multiple layers of refractory ceramic materials, such as clay, are applied to the exterior of the wax pattern. Upon heating, the wax melts and flows out, resulting in a hardened ceramic shell. This ceramic shell is then fired to remove any residual wax and to strengthen the shell. Molten metal is poured into the ceramic mold, and after the metal cools and solidifies, the ceramic shell is broken away to reveal the finished metal casting.
The term “investment casting” originates from the process of heating and melting the wax within the mold shell. Investment casting is often preferred over other casting methods due to its high dimensional accuracy and superior surface finish. It is capable of producing thin-walled components or parts with complex internal and external structures. Unlike sand casting, investment casting does not require draft angles.
Investment casting is suitable for a wide range of materials, including carbon steel, alloy steel, stainless steel, and non-ferrous metal alloys such as aluminum and copper. In the field of hot working, it is particularly useful for manufacturing parts that are difficult to source or form, as well as for components that are costly to produce through forging. Within the casting industry, investment casting can replace other casting methods for certain products, thereby reducing machining allowances, lowering costs, and enhancing dimensional accuracy, surface finish, and mechanical properties of the material. This ultimately leads to an upgrade in product quality.
Advantages of Investment Casting
Investment casting is capable of producing parts with high surface precision and the ability to manufacture complex shapes. It is an ideal choice for customers with specific requirements for dimensional accuracy, surface smoothness, and the design of small-to-medium-sized components;
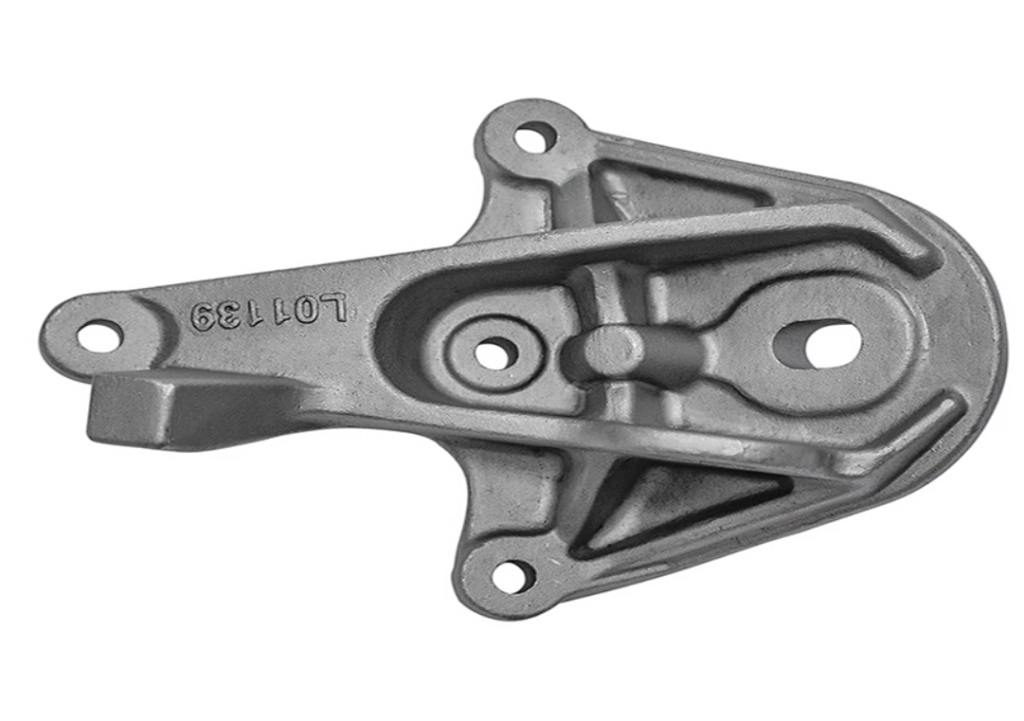
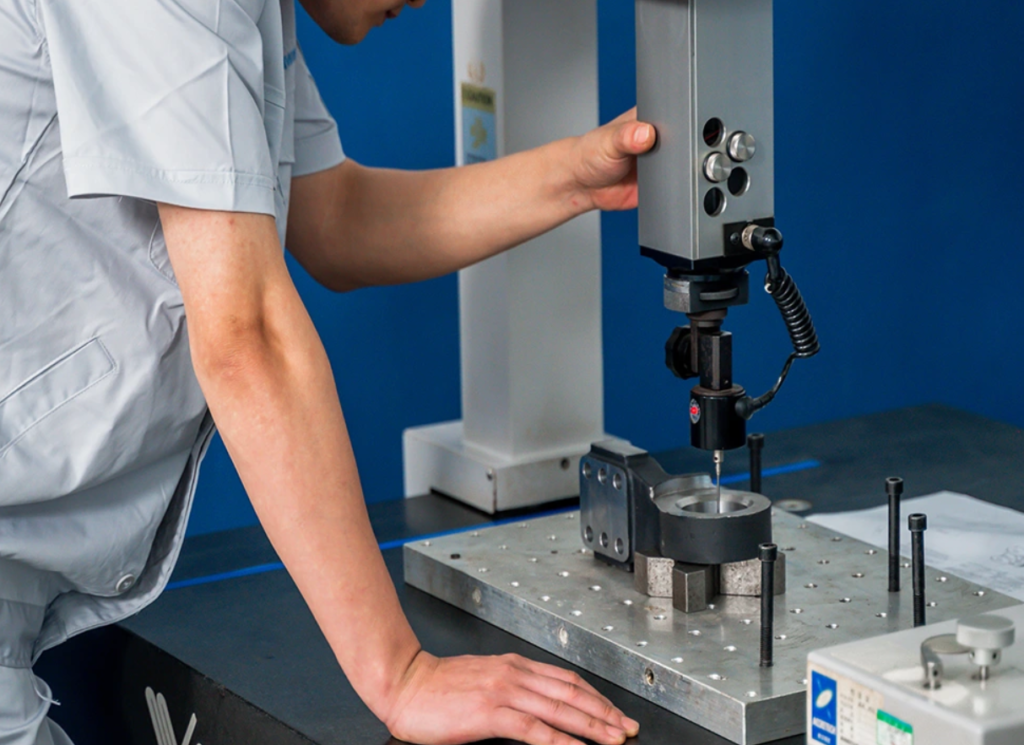
High Precision
The ability to produce parts with complex shapes and high precision
Wide Range of Sizes
Investment casting is suitable for both large and small castings
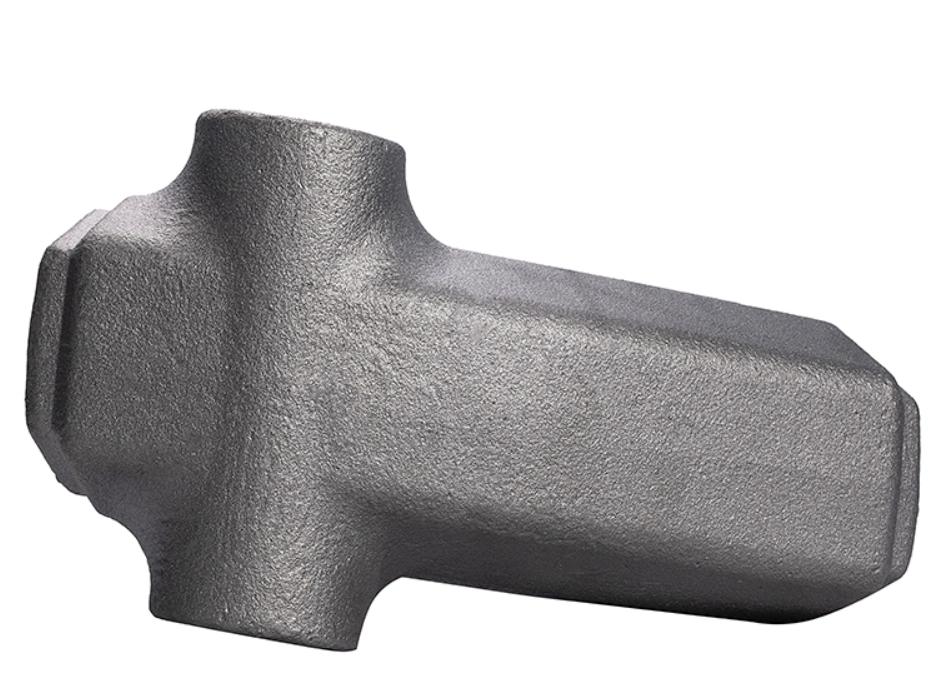
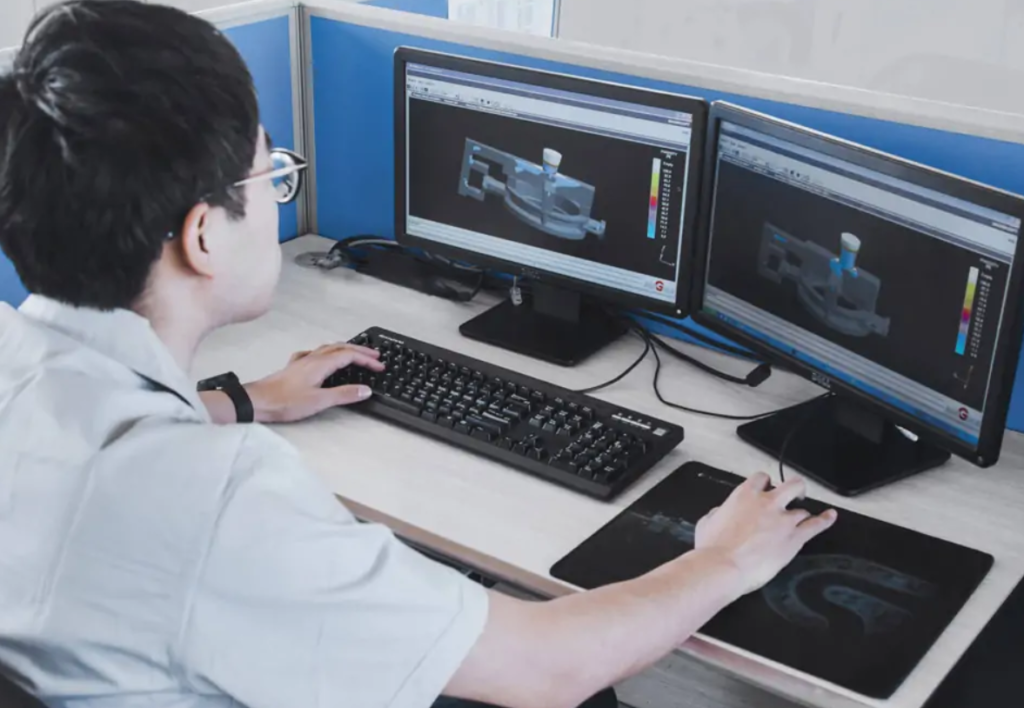
Surface Finish Excellent
surface quality, reducing the need for subsequent machining operations
Design Freedom
The ability to achieve complex structural designs
Investment Casting Workflow
The investment casting process consists of several steps: metal mold manufacturing, wax pattern production, shell mold manufacturing, casting, sand cleaning and cutting, and grinding and finishing.
1.Metal Mold Manufacturing
Since wax patterns and shell molds are destroyed during the investment casting process, a new wax pattern is required for each casting. Therefore, molds for producing wax patterns are necessary.When manufacturing molds, it is essential to consider and calculate the shrinkage rates, which are reflected in the wax patterns, shell molds, and during the casting process.
2.Wax Pattern Production
The number of wax patterns is always equal to the number of castings to be produced, as each casting requires a new wax pattern.Hot wax is injected into the metal mold and allowed to cool and solidify. For complex internal structures, ceramic cores are used to form functional internal features. The wax pattern is an exact replica of the part to be produced, and the production process is similar to die casting, except that liquid wax is used instead of molten metal.
3.Wax Pattern Assembly
Several wax patterns are welded onto a wax sprue to form a wax pattern assembly, creating a gating system. This gating system includes gates, which serve as the entry points for molten steel into the casting system in the next step of shell mold production.
4.Shell Mold Manufacturing
The wax pattern assembly is dipped into a silica slurry, repeated five to six times. Before each dip, different refractory materials are applied, and each layer is allowed to dry and harden. The dried layers form a ceramic shell around the gating system of the wax pattern. The ceramic shell is then heated to melt and remove the wax, creating a hollow cavity. This completes the production of the shell mold, and multiple such shell molds are used in investment casting.
5.Casting
The shell mold is preheated to approximately 800-900°C. This heating process further strengthens the shell mold, removes any residual wax or impurities, and evaporates moisture from the shell mold.Raw materials (scrap steel) are melted in a medium-frequency induction furnace, and alloying elements are added according to the specific material requirements for each heat. Once the molten steel reaches a temperature of 1530-1580°C, it is ready for casting. The molten steel is poured into the preheated shell mold through the pouring gate and flows through the gating system into each cavity of the assembly. The preheated shell mold facilitates the flow of molten metal through thin or elongated sections. After cooling and solidification, high-precision castings are obtained.
6.Sand Cleaning and Cutting
After the shell mold and casting have fully solidified and cooled, vibration equipment is used to separate the shell mold from the casting. Following initial sand cleaning, shot blasting is performed to remove any adhered sand from the surface of the rough casting. Individual castings are then separated from the gating system using various cutting methods.
7.Gate Removal and Finishing
The gate remnants on the rough casting are removed, primarily through grinding with a grinding wheel or by machining. This process is divided into initial grinding and finish grinding, with care taken to avoid damaging the casting itself. Subsequent finishing involves repairing potential surface defects on the casting, such as sand holes, slag inclusions, flash, burrs, blisters, and deformations. The main methods used for this purpose include grinding, welding, reshaping, and shot blasting.After passing visual inspection, the castings are transferred to the heat treatment production line for various heat treatment processes.
Investment Casting—Manufacturing Process
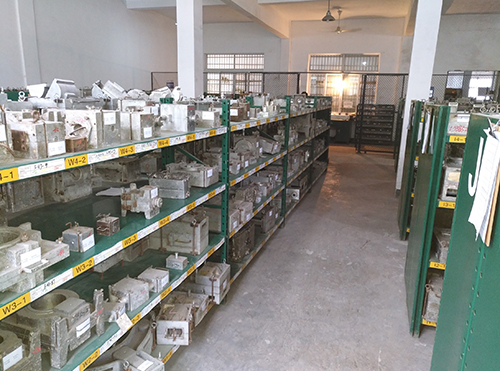
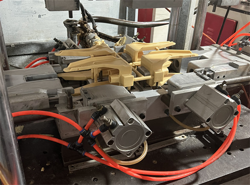
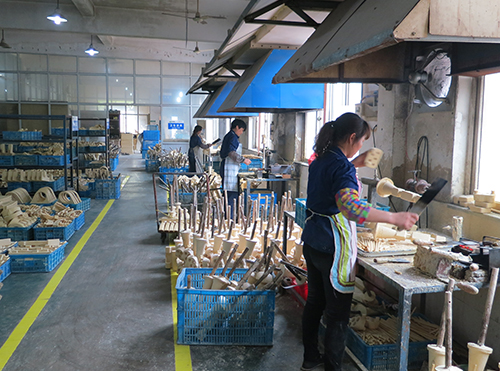
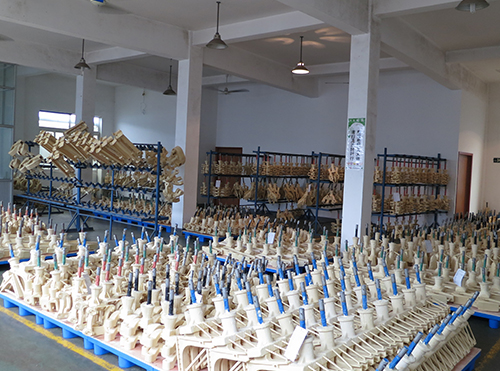
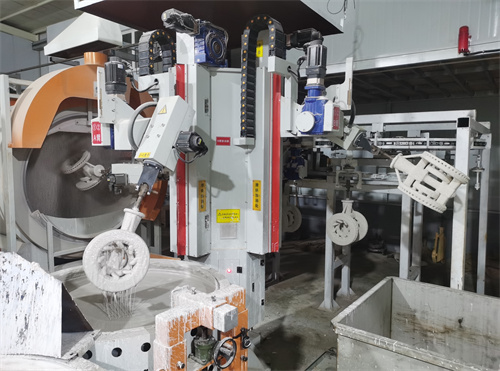
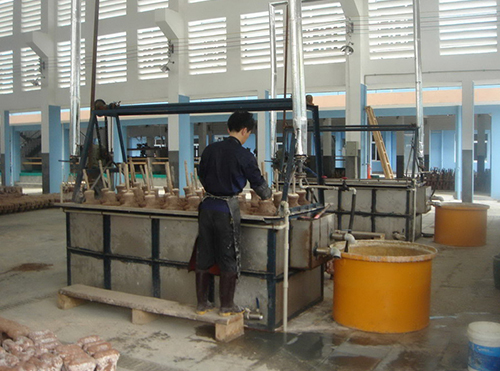
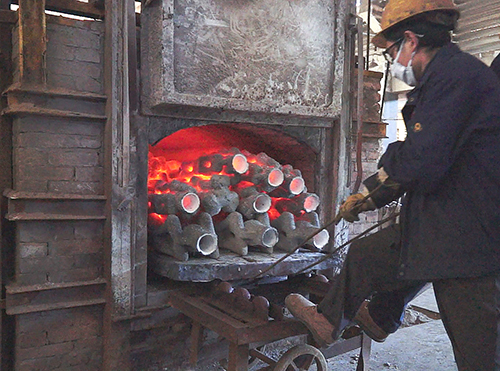
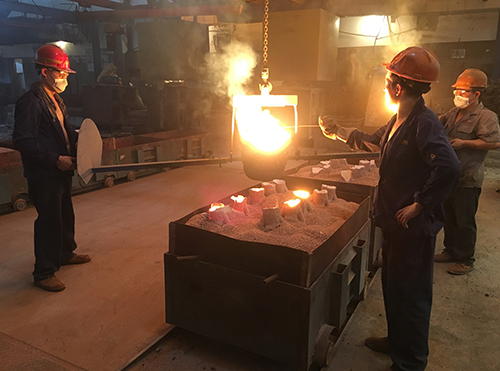
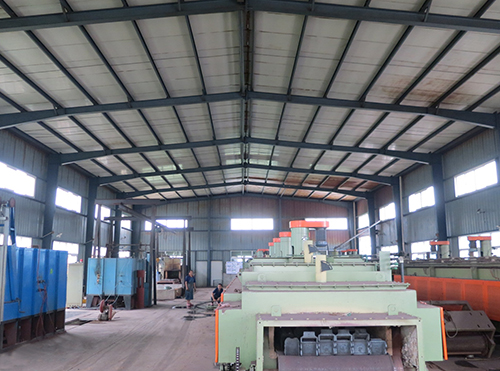
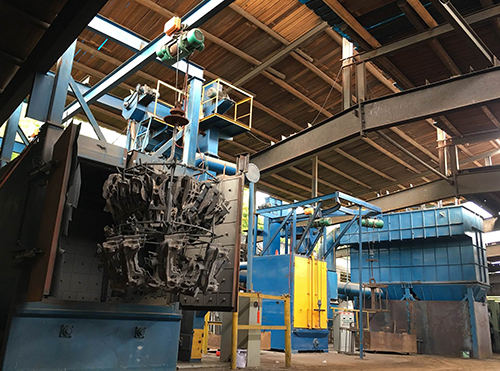
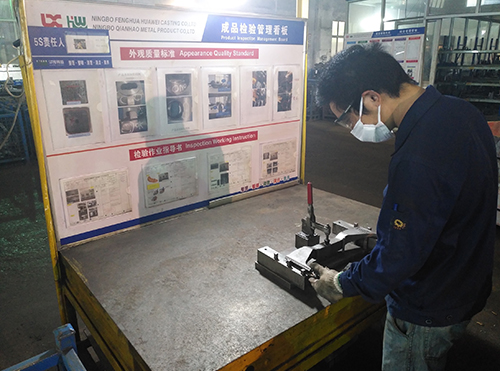
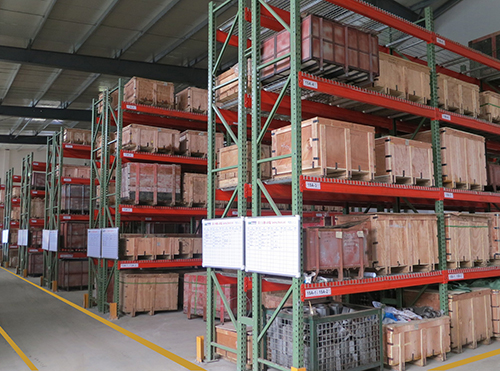
Main Equipment
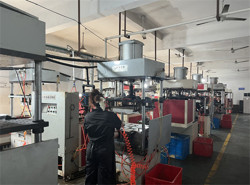
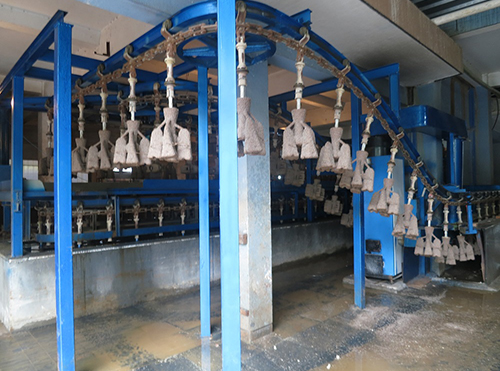
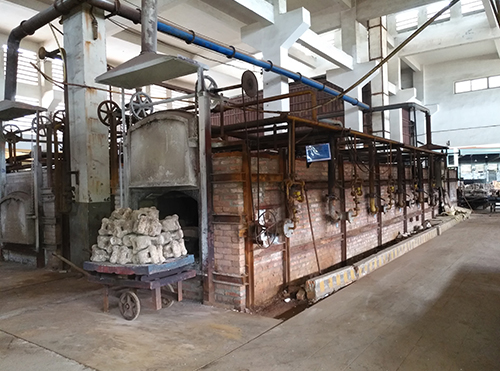
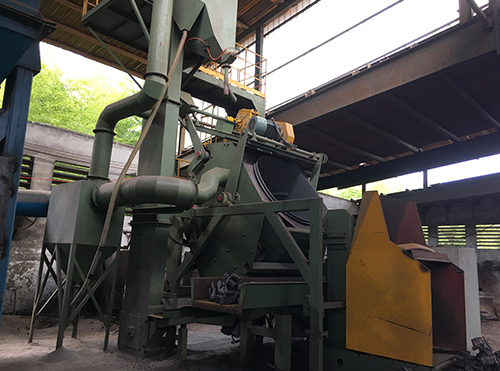
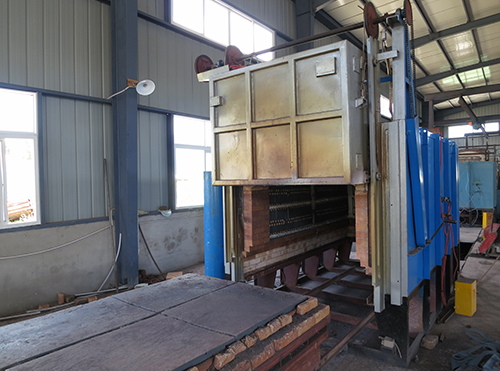
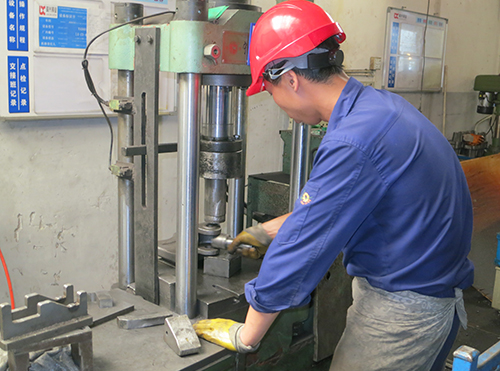