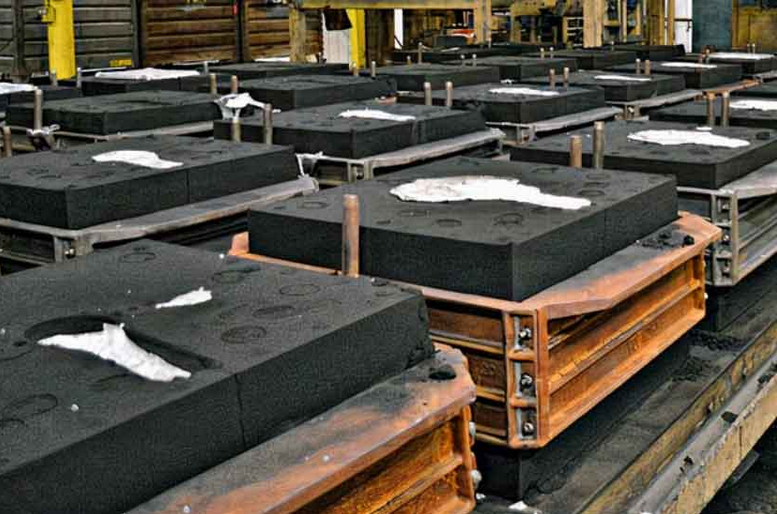
Resin sand casting, also known as no-bake sand casting or furan sand casting, is a versatile and widely used casting process that involves creating molds using a mixture of resin and sand. The process is suitable for both small and large-scale production and offers numerous benefits, making it popular in various industries.
Resin Sand Casting Process
- Pattern Making: The process starts with the creation of a pattern, typically made of wood, plastic, or metal, in the shape of the desired final product.
- Mold Preparation: A two-part mold is made using sand mixed with a thermosetting resin binder. This binder is usually furan resin or a urethane resin. The mold consists of two halves – the cope (top half) and the drag (bottom half).
- Mold Assembly: The cope and drag are put together to form a complete mold cavity. The pattern is placed within this cavity.
- Sand Compaction: The sand mixture is packed tightly around the pattern to ensure the mold takes the desired shape and maintains its structural integrity during pouring.
- Pattern Removal: Once the sand has sufficiently hardened, the pattern is removed from the mold, leaving behind a cavity that matches the pattern’s shape.
- Pouring: Molten metal, such as aluminum, bronze, iron, or steel, is poured into the mold cavity.
- Solidification: The poured metal cools and solidifies, taking the shape of the mold cavity.
- Mold Breakout: After the metal has cooled and solidified, the mold is broken open, and the casting is removed.
- Finishing: The casting may undergo further finishing processes, such as trimming excess material, removing any imperfections, and surface treatment.
Advantages of Resin Sand Casting
- Versatility: Resin sand casting is suitable for a wide range of metals, making it a versatile casting process.
- Complex Geometry: It allows for the creation of intricate and complex shapes and designs.
- Cost-Effective: The process is relatively cost-effective for both low and high production volumes.
- Good Surface Finish: Resin sand casting can produce castings with a smooth surface finish.
- Dimensional Accuracy: It offers good dimensional accuracy and tight tolerances.
- Less Post-Casting Machining: Often requires minimal post-casting machining, reducing overall production time and costs.
- Environmentally Friendly: The process does not generate harmful emissions, making it environmentally friendly.